Enhancing Corrosion Resistance in OEM Flow-Assisted Chelation Processes
The integration of flow-assisted chelant corrosion mitigation strategies within Original Equipment Manufacturer (OEM) processes represents a significant stride towards enhancing the durability and performance of industrial equipment. This innovative approach harnesses the power of controlled chemical reactions to protect metal surfaces from degradation, ensuring longevity and reducing maintenance costs.
Chelation, characterized by the formation of complexes between metal ions and organic or inorganic ligands, plays a pivotal role in this context. In the presence of a flowing medium, chelating agents can be strategically introduced to interact with metallic components, forming stable complexes that shield against corrosive attacks. The flow dynamics not only facilitate an even distribution of the chelating agent but also help in removing corrosion products, thereby preventing localized damage progression.
OEMs are increasingly recognizing the value of integrating such advanced techniques into their manufacturing workflows. By fine-tuning the flow rate, concentration, and type of chelating agent used, they can tailor the anti-corrosion properties to specific operational needs. For instance, in applications where there is a constant exposure to moisture or acidic environments, a robust chelation strategy can significantly extend the service life of critical components.
Moreover, the use of flow-assisted chelant systems offers environmental benefits as well
Moreover, the use of flow-assisted chelant systems offers environmental benefits as well
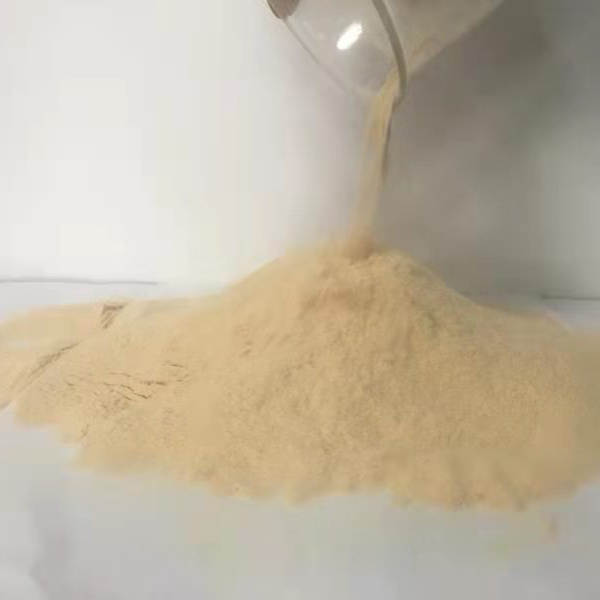
Moreover, the use of flow-assisted chelant systems offers environmental benefits as well
Moreover, the use of flow-assisted chelant systems offers environmental benefits as well
oem flow assisted chelant corrosion. These systems often require lower concentrations of chemicals, resulting in reduced environmental impact compared to traditional corrosion inhibitor methods. Additionally, the improved efficiency leads to less downtime for maintenance and part replacements, further emphasizing the sustainability of this approach.
However, the implementation of flow-assisted chelation requires careful consideration of process parameters and material compatibility. A thorough understanding of the chemical interactions at the metal-ligand interface is crucial for optimizing protection while avoiding any unintended consequences such as accelerated deterioration due to incorrect agent selection or dosage.
In conclusion, the adoption of flow-assisted chelant corrosion control within OEM processes presents a promising avenue for enhancing the resilience of industrial equipment. As research continues to refine our understanding of these complex interactions, it is likely that we will witness more widespread integration of such technologies, heralding a new era in materials preservation and process optimization.